Turntables 101
It can be really daunting when you are looking to buy your first turntable. They can range from a couple of hundred dollars, to thousands and thousands of dollars.
Before you embark on your journey, it might help to understand the components that make up a turntable and how it makes music.

A turntable consists of five basic components:
the platter on which the record rests
the plinth which holds the spindle that the platter can spin freely on
the motor unit which turns the platter
the tonearm which has a smooth moving pivot that holds the cartridge, allowing it to move freely across the record grooves so it can pick up the musical information cut into the record grooves
the cartridge itself
A turntable reproduces music that is stored on a vinyl record by turning the record at a correct and constant speed, and moving a stylus through the grooves of the record. The stylus' tiny movements move an electromagnet inside the cartridge, and these electrical signals can then be amplified through your audio system to generate music.
And that's basically it.
The reason turntables can vary so much in price has to do with the level of engineering and complexity to tackle the problems of each step of the process.
Let's break it down.
Step 1 - Turning the record
The goal here is simple - spin the record at a constant preset speed, usually 33 1/3 rpm, 45 rpm or 78 rpm. And to minimise noise transferred from the motor or the environment to the platter, which could move from the platter to the record. Any rumble or vibration or noise that is transferred across to the platter will get picked up by the stylus as it moves through the record grooves.
Belt Drive vs Direct Drive
Most turntables employ one of two ways of turning the record: belt or direct drive.
The simplest way to turn a platter is of course by bolting the platter spindle directly to the driveshaft of the motor. The motor can control the speed at which the platter turns perfectly. The downside, of course is that motor units are prone to vibrations and these vibrations or rumble could potentially get transferred to the platter, and from there to the record, and stylus.
The alternative is to have the motor unit placed separately from the platter, minimising the impact of the vibrations, and then use a belt to turn the platter. The downside of this approach is that the belt can cause slight variations to the rotational speed, often referred to as wow and flutter.
So both approaches have their benefits and drawbacks. The more expensive turntables try to mitigate these issues with better engineering and materials. The best direct drive turntables use complex and smooth bearing motors that have very little rumble. And the best belt drive turntables use quartz clocks or multiple asynchronous motors and better power supplies to minimise speed variations.
The new Esoteric Grandioso T1 turntable that we have on demonstration at our store takes engineering ingenuity to the next level.
Like belt driven turntables, the T1 employs a separate motor unit that sits insulated and independently of the plinth. The motor unit uses an external crystal clock to maintain accurate speed timings, but it uses matching magnets on the motor and platter to turn the platter, but it remains contactless. The matched magnets ensure a perfect speed every time.

The result is truly the best of both worlds.
Now that you have the platter spinning, you need to watch out for other sources of vibrations. These could come from air borne vibrations such as when you are playing the music too loud, or even from the floor, especially when you have floating floors.
Some turntables, like Avid or Linn will suspend the platter on springs to minimise the effect of vibrations. Others like the Esoteric will use special damping mechanisms on their support feet. Most turntables will also often include a really heavy platter that is more impervious to vibration, especially from air borne vibration. The platter on the Esoteric Grandioso T1 weighs almost 20kg.
Step 2 - Putting the Stylus into the Grooves
The next step of playing a record is a way of mounting the cartridge on an arm that can move freely over the record as the platter is spinning.
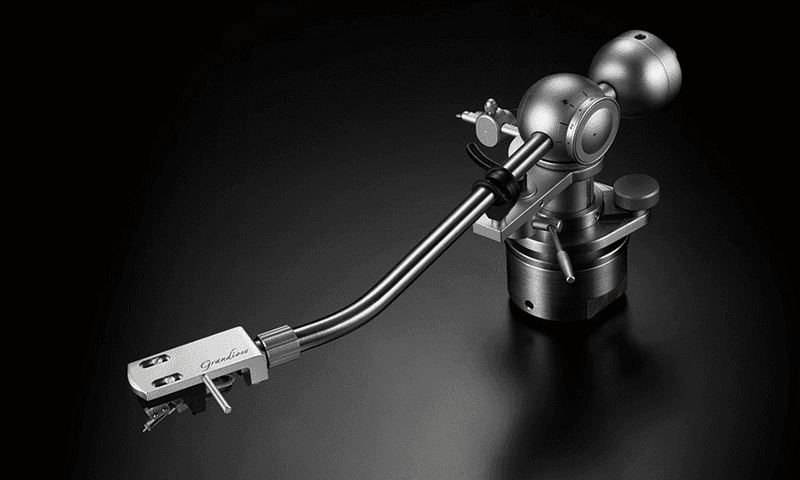
The best tonearms use special bearings or pivots that offer minimal resistance to motion. This means that the stylus is able to pick up the music that is cut into the grooves of the record. If a tonearm does not offer free motion, it could hinder the stylus from picking up the smallest details of the music. This is why you usually do not find fully automatic turntables in the best turntables. Fully automatic turntables use belts and gears to lift and move the tonearm in place automatically, and offer a convenience, but it is at the expense of the tonearm being able to move freely and smoothly.
You will also find use of exotic materials, such as carbon fibre, titanium, in tonearms that offer improved rigidity and maintain a light weight, so as not to intrude on the stylus' ability to react to grooves cut into the records.
The other aspect of the tonearm to consider is minimising tracking errors. Ideally, the tonearm should be aligned tangentially to the circular record grooves. With most tonearms, the tonearm is only perfectly tangential at two points of the record. And there are small variations in the angle outside of these two points. Using a longer tonearm can minimise the errors in tracking. This is why the best turntables might use a 10" or even 12" tonearm. But having a longer tonearm also means a heavier arm, that will impose a bigger load on the bearings and pivot, plus it also requires the cartridge to have a better compliance to cater for the higher weight of the tonearm.
An alternative design to tonearms are tangential tonearms.
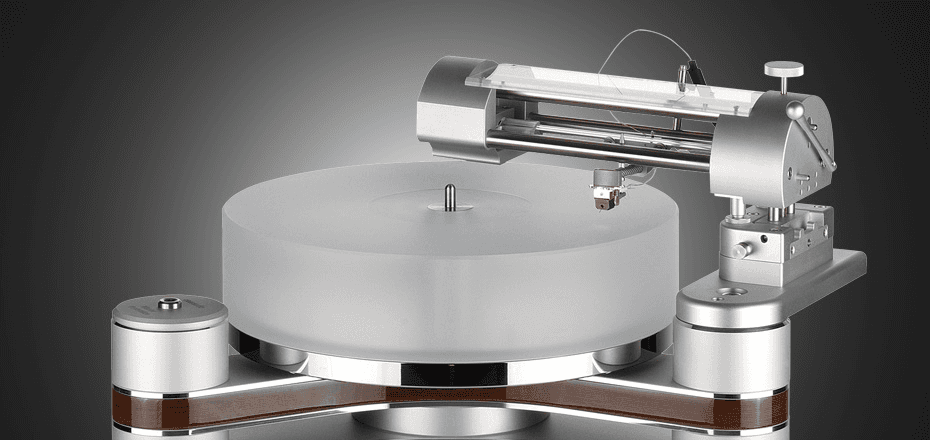
These will track the record grooves perfectly tangentially but it does require more maintenance to ensure the rails are dust free, and can move smoothly
Step 3 - Feeling the Grooves

Moving Coil vs Moving Magnet
It helps to think of a turntable cartridge as a tiny electromagnet generator. You can create tiny electrical signals in two ways:
when you move an electrical coil inside a magnetic field, or
when you move a magnet inside an electrical coil
So the stylus can be connected to the magnet or to the electrical coil. This results in the two major forms of turntable cartridges - moving coil or moving magnet.
Moving magnet cartridges are easier to manufacture since the coils do not move and are fixed to the body of the cartridge. It also has the benefit of being able to swap out the stylus when it gets worn out over time, since the magnet is not wired to the body. Lastly, moving magnet cartridges also generate higher voltage levels (millivolts rather than microvolts) and are easier to amplify. The downside to moving magnet designs is that the magnets are relatively heavier, and thus the stylus may be less sensitive to tracking the grooves of a record. The overall sound might come across as warmer without a lot of high frequency extension.
Moving coil cartridges are more complex to manufacture because the stylus is connected to the electrical coils, and these are then connected to the 4 terminals of the cartridge. The benefit is that the stylus is connected to a lower mass and is thus better at picking up details in the record grooves. The voltage levels are much lower (microvolts) so they need a phono preamp stage capable of handling MC cartridges to work properly. The benefit is that you get much better clarity in higher frequencies with moving coil cartridges.
Diamonds are (almost) forever
Another factor on why some turntable cartridges cost so much has to do with the stylus being used.
The cheaper cartridges use a conical stylus tip, or an elliptical one which is cheaper to make. The more expensive ones like a Shibata or Micro Line stylus have narrower profiles and often use a real diamond which is cut to a very specific shape and size.
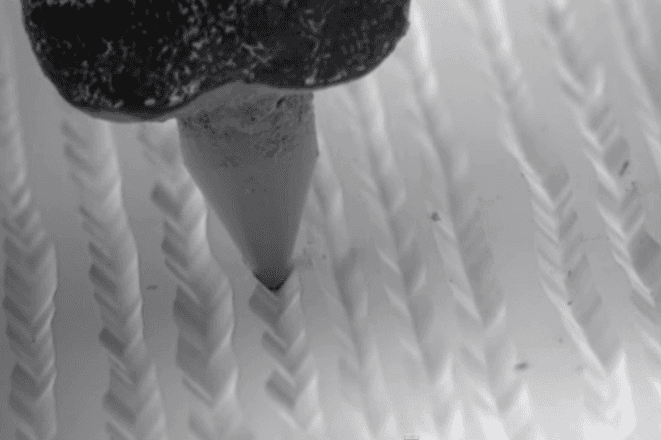
The shape and size of the stylus tip affects how much of the groove it is able to come into contact with, so the slimmer profiles can often retrieve micro details of a recording that might otherwise be lost with a broader profile stylus.
So what does this all mean
I hope this primer helps you understand what goes into the design and manufacturing of a turntable. It is a very intricate piece of equipment. If you have more questions, feel free to drop by our store to discuss what types of turntables might work best in your system.
Remember that a lot of records today are irreplaceable - and you want to get a turntable that not only plays these records but also minimizes damage or wear and tear on these records.